Printed Stand Up Pouches--The Workhorse
Tell me more
Printed stand up pouches continue to be the workhorse or one of the workhorses in the flexible retail packaging landscape. The printing capability for consumer awareness on top of the barrier properties that stand up bags can be made from make this retail packaging hard to beat.
Because the general term “plastic” is so frowned upon, companies are looking to other substrates and laminated materials but in actuality (not all cases) they could be making matters worse. The different material structures will be outlined in further detail
below. While there are other materials that are available for printed stand up pouches, it’s important to know if these materials can be recycled, can they biodegrade, and are they landfill friendly?
Stand up pouches are made from laminated barrier films based upon a number of criteria pertaining to the product. What is being packaged, how much weight is in the package, are the contents susceptible to damage from moisture, vapor, odor, sunlight or any number of other factors? With this in mind, printed stand up pouches are engineered to protect the contents first...and then provide maximum printing “real estate” for a company to tell their story and build their brand.
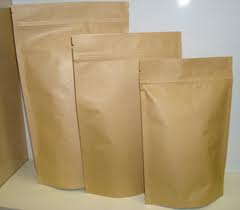
Printed stand up pouches can be made from a number of different materials...we’ll explore them all.
Paper
- Printed stand up pouches made from paper are all the rage now because the perception from consumers is the paper is better for the environment. However, paper, by itself...like the paper in a grocery shopping bag, has no barrier properties whatsoever...none. Plus, have you ever seen paper shopping bags printed...the paper itself is very porous and doesn’t allow for high quality, bold printing.
- In order to make printed stand up pouch retail packaging look more appealing, manufacturers are laminating materials to the paper...these laminates are almost always, plastic...like a clear plastic, or even a foil structure. The lamination layer is often the printed layer (so it looks like the paper is printed but in reality, it is the plastic layer that is printed). Once paper is laminated with another structure that is not..this package is no longer recyclable...as there is no way to separate the laminated layer from the paper layer. Again...this attempt to be more “earth friendly looking” actually makes things worse
Plastic
- Layers of plastic are the most common for printed stand up pouches. Clear film can be printed and laminated as well as provide barrier properties to protect the contents. Printed clear film is very common and the packaging has been used in the retail landscape for years.
- Did you know that printed stand up pouches made from clear film is recyclable? Seriously? This film can be ground up and used as filler or regrind for other plastic products like park benches, bumpers, plastic lumber, or children’s toys.
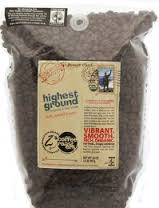
Foil
- Foil used for retail packaging has been around what seems like forever. But foil, by itself is very flimsy and weak...it’s got to be laminated to other materials...very much like clear plastics. Now, foil provides excellent barrier properties, but it isn’t incredibly strong or durable. Just like the foil you use when cooking, foil when folded or creased doesn’t bounce back or rebound and quite often that reduces the strength of the structure. Foil is one of the most expensive materials because of its barrier properties however other materials such a metalized film (known by the trade name Mylar) has grown in popularity.
Mylar—
- Mylar is a trade name for metalized film. Metalized film is one of the more popular barrier films used for printed stand up pouches because it is a naturally opaque material and as a result printing really “pops”. Another benefit of Mylar is that fact
that the film is very durable and resilient. When bent or folded metalized film will rebound and respond instead of showing noticeable creases and folds (like foil does)
Compostable—PLA-Biodegradable
- This is the newest structure that has hit the printed stand up pouch market. As I described above regarding paper itself, this material uses a kraft paper base and then is coated/laminated with a PLA material that provides some barrier properties and allows the entire bag to biodegrade when exposed to air and sunlight. There are problems with this material and design. Some countries overseas are NOT happy with PLA coatings and materials because of the out-gas that comes when it is
exposed to air and sunlight. Some countries have BANNED PLA coated products completely. However, in the US, printed stand up pouches with a PLA coating are accepted (for now). Issues are that these bags are not very strong or durable, so they don’t do well with heavier loads (over 1 pound) and the print quality is average at best. Many companies who want to use this type of substrate and have an attractive print scheme often start with a white kraft paper so the printed colors look more appealing
PROBLEMS AHEAD:
- Keep this in mind, when using laminated materials that are of the same “family”...clear film and metalized or foil...they all play well together and can recycled in landfills and most often have a recycle symbol of an R7. When paper is involved...like regular kraft paper or even compostable paper...these items cannot be recycled together...at all.
- Dirty little secret...everyone wants to help the environment. However, in the US, when our garbage goes to the recycler no one can tell if the film is laminated with other materials (making the recycling an R7) or a pure recyclable material...like the blue shopping bags we get from the grocery store. If there was a controlled system to identify whether a film is laminated or not...or what the materials are in the laminated film, the recycling company could easily identify and group the materials accordingly. ..there is NOT...so ALL plastic that goes to a recycler (unless in a controlled system that only recycles a certain type of plastic film…very, very rare)...ALL plastic is ground back up and considered an R7 or regrind.
- Dirty little secret 2...when we send our garbage to the landfill...garbage stinks...it smells. Because garbage smells, the first thing the landfill does when garbage gets there is to bury the garbage to control and eliminate the odor. Once garbage...of ANY kind is buried...nothing is exposed to air or sunlight....so nothing can biodegrade...The point, you could have the most elaborate eco-friendly material but if it cannot be exposed to air or sunlight, nothing will biodegrade. All of these materials and coatings are a waste of time…sorry to tell you that but it’s true.